OTR Tire Factory
Forlander OTR tire factory is driven by the cutting-edge intelligent manufacturing system to optimize and innovate the OTR tire manufacturing process. This intelligent system integrates production automation, data analytics and artificial intelligence to reduce production costs, improve production efficiency and reshape production methods. This makes Forlander the leading OTR tire manufacturer in China tire industry who manufactures port tire, forklift tire, mining tyres, agricultural tire, and more.
Table of Contents
Forlander Inteligent OTR Tire Factory
We are constructing our OTR tire intelligent manufacturing factory according to Industry 4.0 standards, utilizing advanced equipment and self-developed specialized machines, optimizing manufacturing processes, and aiming for flexible production of personalized custom orders.
The OTR tire intelligent factory integrates the world's most advanced information and communication technology, digital control technology, and intelligent equipment technology. It innovates the original tire manufacturing processes, achieving optimized control and automated management of over 30 process flows including intelligent sorting, testing, transportation, and warehouse management.

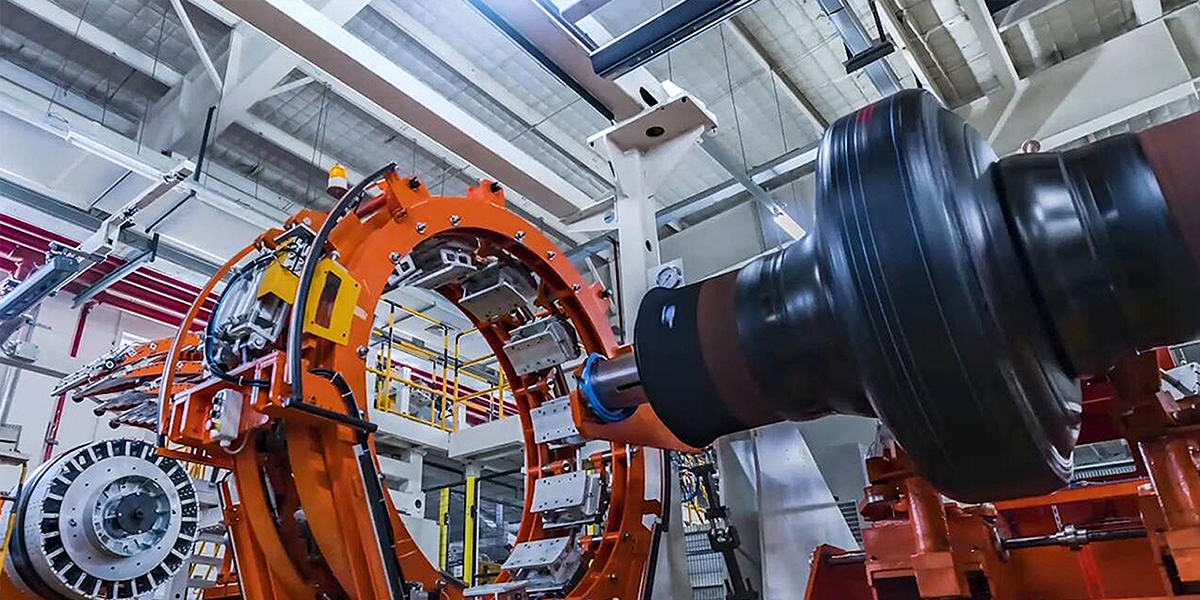
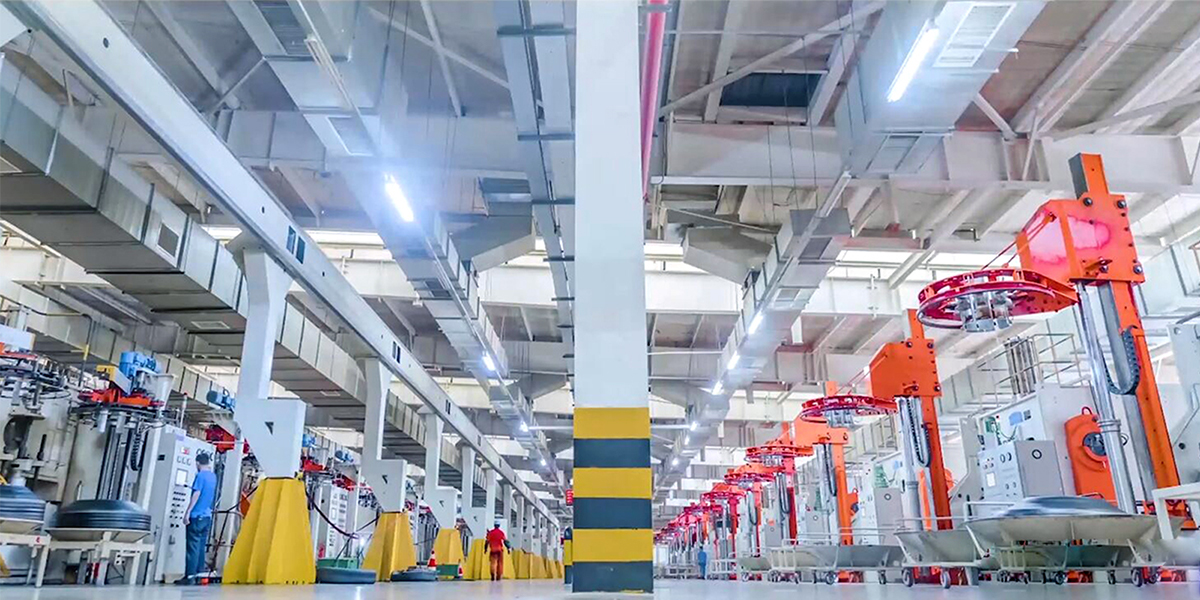
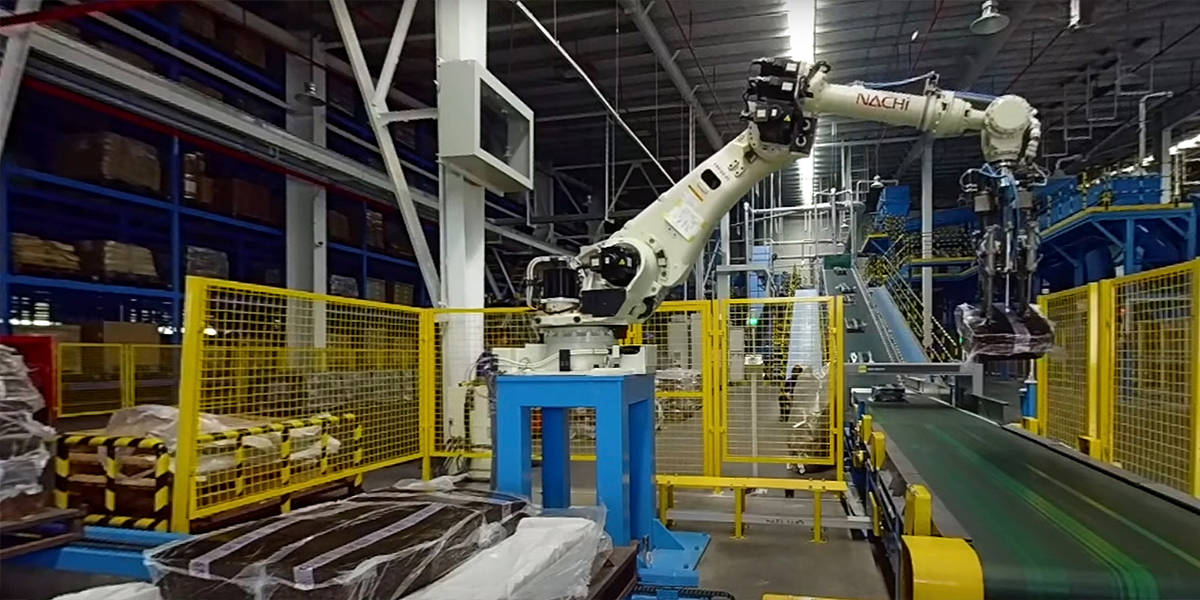
Forlander OTR Tire Manufacturing Execution System (FOTMES)
Forlander OTR Tire Manufacturing Execution System (FOTMES) achieves full visualization of OTR tire automatic production and information management. The FOTMES achieves 98% automatic collection of process data, 96% automatic control commissioning rate, 80% reduction in defective product rate, and 200% increase in labor productivity. Forlander's intelligence level has significantly improved, and tire quality has reached a high-end global standard.
The core of intelligent manufacturing is rapid on-demand manufacturing based on product modularization and lean production. It integrates and develops the world's most advanced information and communication technology, digital control technology, and intelligent equipment technology to achieve enterprise interconnection, organizational unitization, processing automation, production flexibility, and manufacturing intelligence.
The automatic collection of project production process data has reached 98%, and the factory's automatic control commissioning rate exceeds 96%. The entire production process is transparent and visualized, establishing a unified platform for full life cycle data. This enables intelligent customization, production scheduling, feeding, detection, warehousing, and evaluation. After implementing the project, operating costs will be reduced by approximately 30%, product development cycles will be shortened by about 50%, defective rates will be reduced by over 80%, labor productivity will increase by 200%, and energy utilization will improve by about 30%.
Intelligent Logistics Management System
The integration of an intelligent warehouse system has significantly improved storage efficiency by combining information flow with logistics. This system effectively reduces inventory in the production process while ensuring the quality of tire parts and semi-parts.
Forlander Tires has incorporated top-notch equipment, including Automatic Guided Vehicles (AGV) from Sweden, 3D truss robots, ABB joint robots from Switzerland, and other renowned international brands. Our advanced logistics system seamlessly connects all production procedures, enabling high-efficiency, fast, intelligent, and reliable process lines. The intelligent logistics system facilitates automatic material requisition, fixed storage, precise transportation, and real-time feedback, resulting in enhanced productivity and streamlined operations.
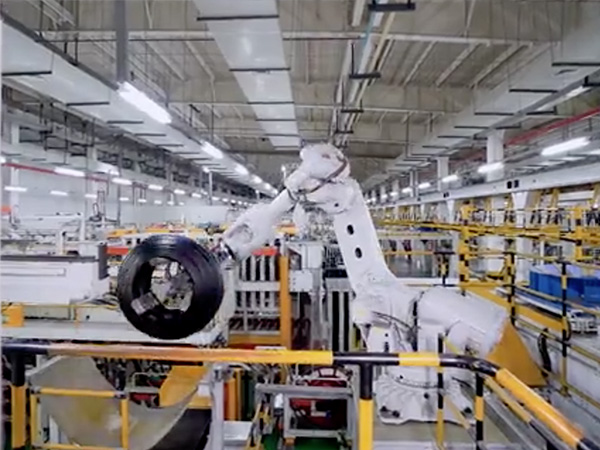
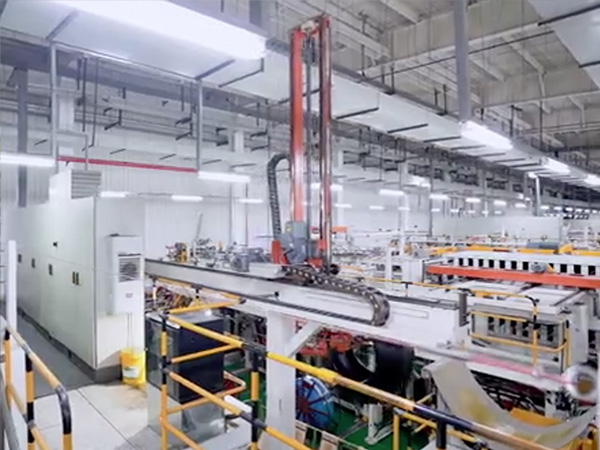
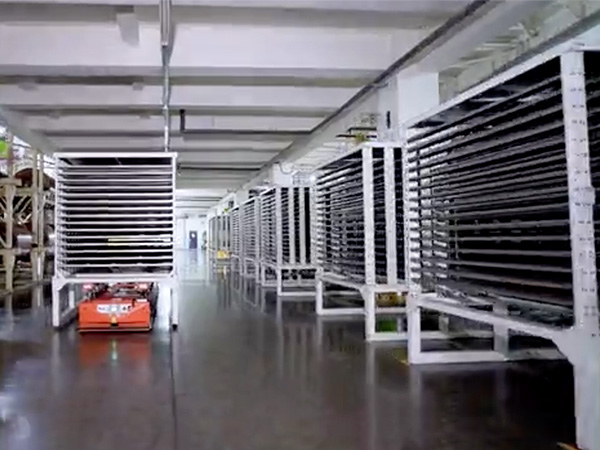
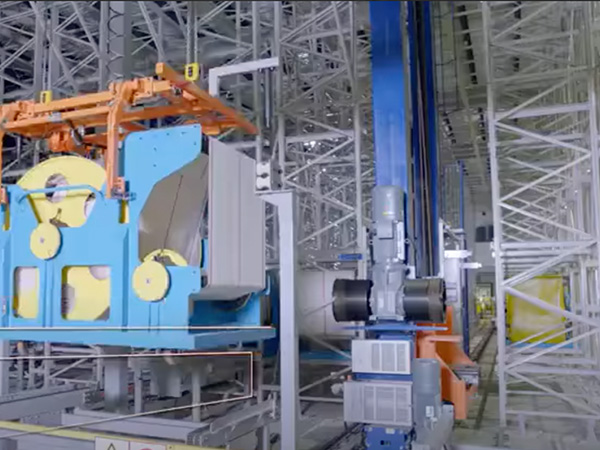
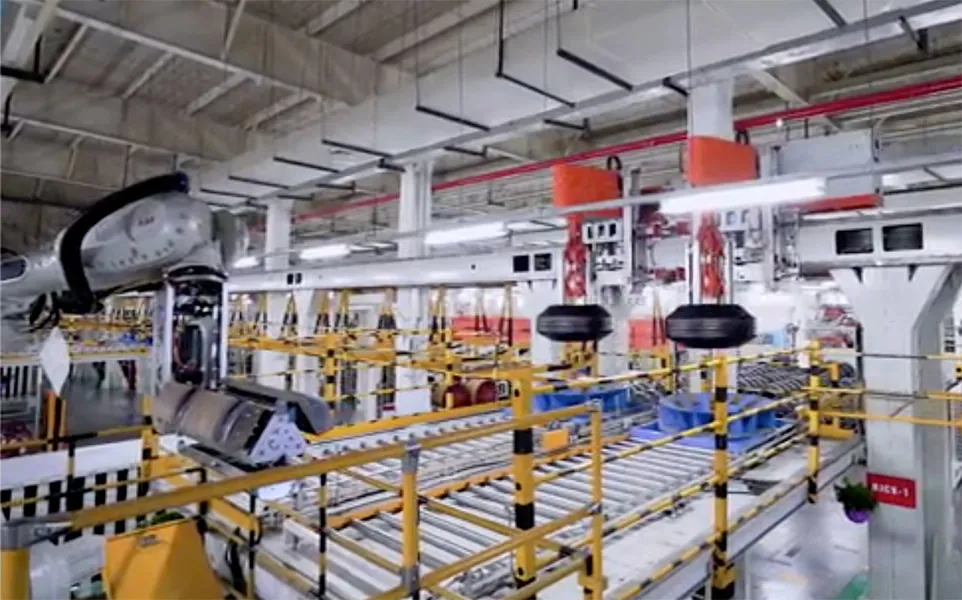
5 Steps to Manufacture Premium OTR Tires
Raw Material Mixinging
Forlander Tire has incorporated the Japanese Kobelco BB430 high-efficiency internal mixer to enhance the quality and efficiency of rubber mixing. This mixer utilizes 6WI and 4WN high-efficiency shearing rotors, along with high-efficiency meshing rotors, to comprehensively improve the quality and efficiency of the rubber mixing process. The quality of the rubber material plays a crucial role, accounting for 80% of the internal tire quality.
OTR Tire Extruding
The OTR tire tread is autonomously gathered by a grid car and transported using an AGV (Automated Guided Vehicle) to eliminate human errors, ensuring the tire tread's quality and enhancing tire uniformity.
OTR Tir Forming
The Forlander Intelligent Building Machine is the world's highest-performing intelligent building machine, serving as the most crucial equipment for enhancing tire uniformity.
The OTR tire building speed is increased by 25%-30%, resulting in a remarkable 56.5% improvement in working efficiency per capita. As a result, the daily output exceeds 450 pieces of OTR tires. Furthermore, OTR tire bead wire significantly reduces the production time from 69 seconds to just 23 seconds.
OTR Tire Curing
Cutting-edge full hydraulic B-type double-mold vulcanizer is appied for the curing process of OTR tires. This vulcanizer is equipped with an automatic logistics system, ensuring ultra-high precision, fast loading speed, and full-process automation. Additionally, we prioritize regular maintenance to ensure the optimal performance and longevity of the equipment.
OTR Tire Inspection
Online OTR Tire inspection is the final OTR tire manufacturing process to check the off the road tires using online or real-time inspection systems. These systems utilize advanced technologies such as machine vision, sensors, and artificial intelligence to assess the shape, defects, surface, dimensions, and structural integrity of OTR tires during production.
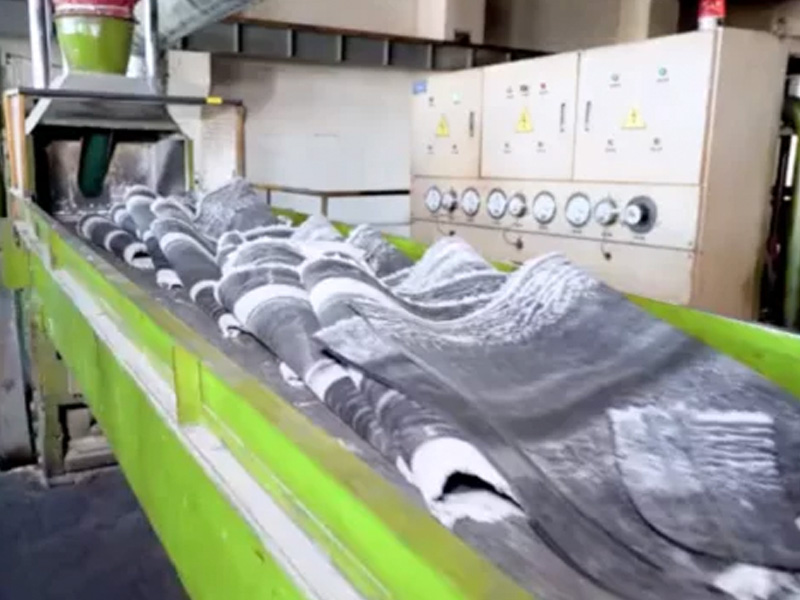
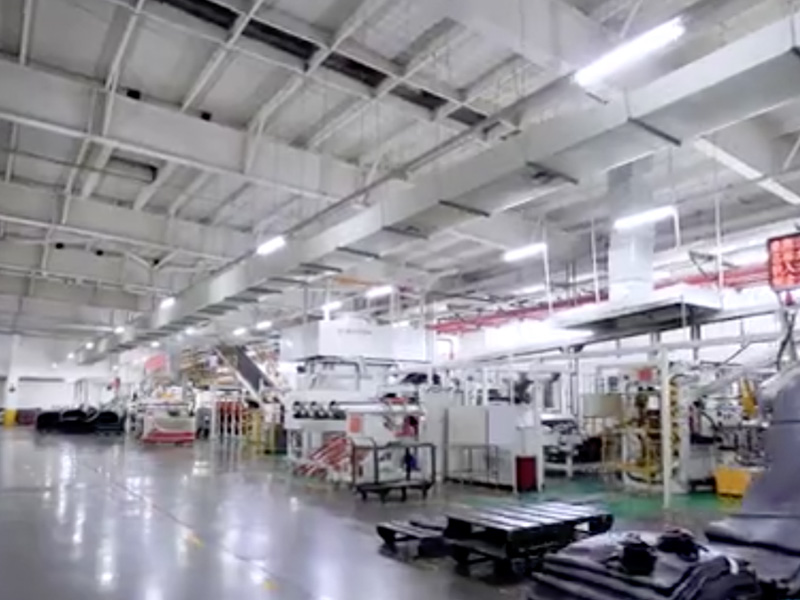
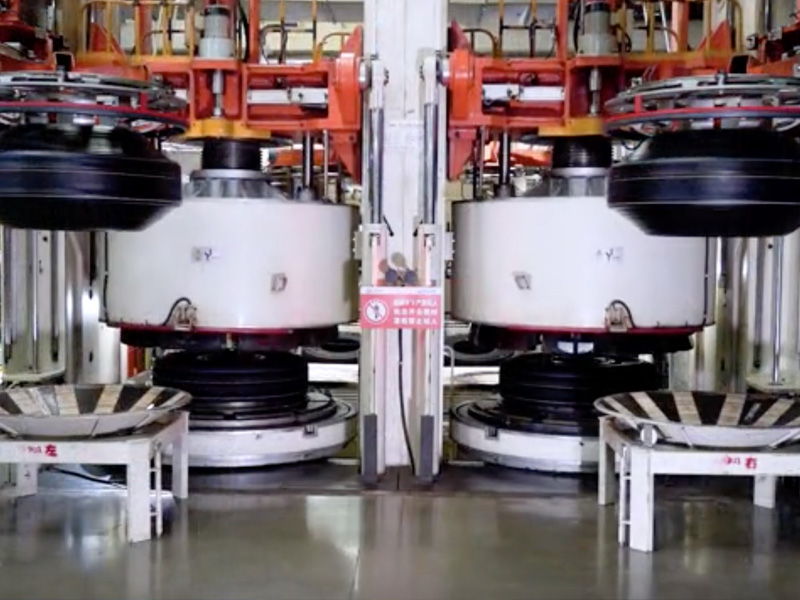
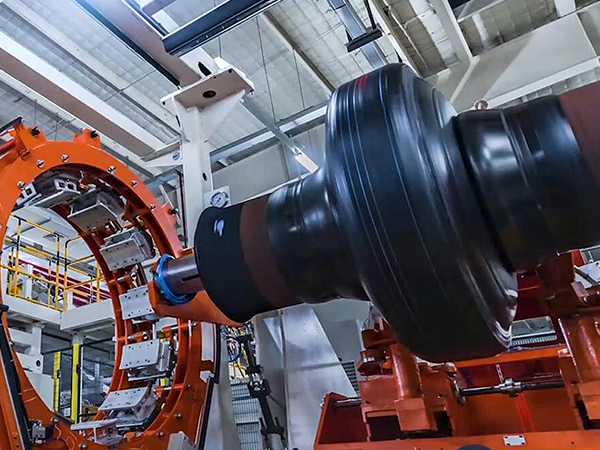
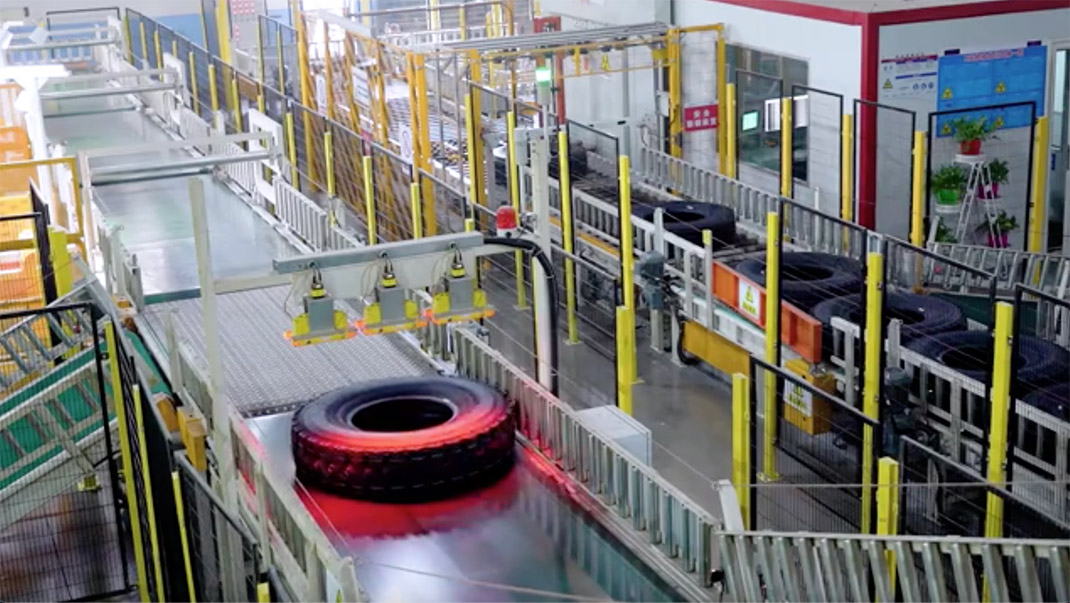
Quality Control System in OTR Tire Factory
Dynamic Balance Tire Tester
The Dynamic Balance Tire Tester is a specialized machine used to accurately measure tire imbalances. This machine detects any errors in the tire's balance and allows for immediate correction, ensuring improved stability and overall tire performance. By identifying and addressing imbalances during the testing process, the dynamic balance tire tester effectively enhances tire quality and work efficiency. This helps to prevent issues that could arise from imbalanced tires, such as vibrations and uneven wear, ultimately contributing to a smoother and safer driving experience.
X-ray Tire Machine
Forlander Tire utilizes fully automated modular X-ray inspection systems for tire quality control. These systems conduct internal inspections of the tire components to detect any underlying defects that may occur during initial use. The aim is to ensure that all tires are structurally sound and reliable immediately after production. By employing X-ray technology, Kunlun Tires enhances the quality assurance process, identifying potential issues that may not be visible from the exterior of the tire. This thorough inspection helps to deliver tires that meet high standards of safety and performance.
American Akron Uniformity Tire Tester
The American Akron Uniformity Tire Tester is a fully automatic machine designed for 100% tire checking during production, aimed at ensuring tire quality. This advanced tester performs comprehensive tests to assess tire uniformity, detecting any deviations or irregularities that could impact the tire's performance and safety. By conducting thorough inspections on every tire, the American Akron Uniformity Tire Tester helps maintain high standards of tire quality and reliability.
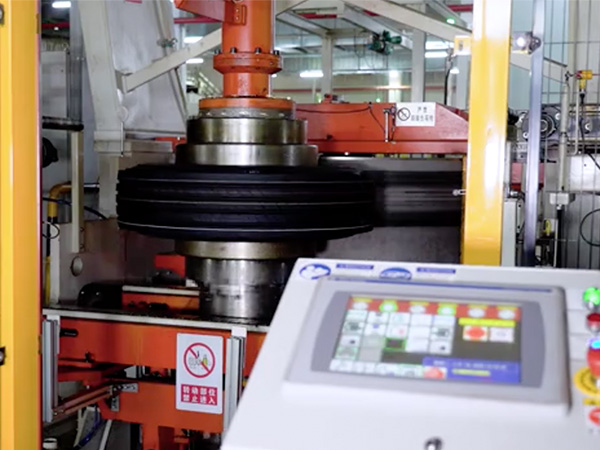
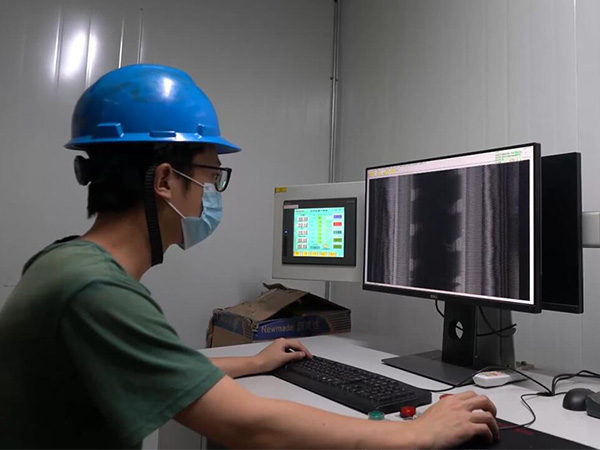
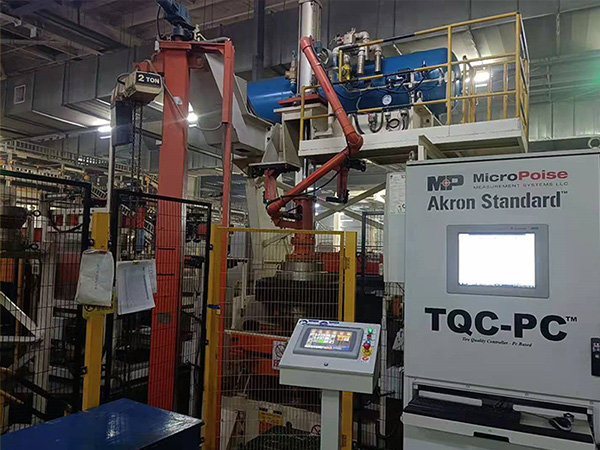